Junior's Numismatic Lesson of the Day: Problems of the Early Mint
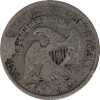
The Early Mint was plagued with problems and growing pains during the late eighteenth century. It took the Mint many years to iron out all the details and settle into better and better methods of minting coins. The planning required for minting coins in those first forty or so years ago was lengthy and complex. The technology used in the Mint was extremely sophisticated for its time, and only surpassed by the technology used by the military for making firearms.
One of the biggest problems the Mint had, was finding quality Tool Steel for dies. While we consider steel to be a very common material now, even as late as 1900, only a small percentage of iron mined was turned into steel, and even that was usually low quality and expensive. Phosphorus and sulfur were often a big problem in this steel. It would make the steel too brittle, and thus it would break very quickly, either during the process of making it into dies, or it would have terminal problems after striking only a few coins. Benjamin and William Huntsman of England, a father and son firm, created a process for making higher quality steel. They refined blister steel to make a more uniform and homogeneous steel. They also used Swedish iron, which was low in phosphorus and sulfur. This new steel was much more effective, but could still be prone to problems if the die was prepared wrong.
The making and preparation of a die was time consuming and expensive. So, the Mint did everything they could to salvage worn out dies. Old dies would be brought back up to the engravers. They would then lap it on a surface plate with a fine pumice or rottenstone with some cutting fluid. This was a very effective technique for removing clash marks and orange peel effect from the fields. Sometimes lapping made the first few coins struck with the die again appear proof-like. Sometimes, an engraver would get to aggressive with the lapping, and there would be loss of shallow details. This has been known to cause floating berries, shafts of arrowheads to disappear or appear thinner and loss of curl detail. Stars also appear to become smaller and farther apart from each other after lapping. If necessary, an engraver would also rework portions of the die to add lost details.
Rusting was also a problem when storing dies. Wax was commonly used as a rust preventative, but some dies still became rusted while in storage. This caused the dies to become severely pitted. Sometimes, a lapping would remove the pits and would make the last few pieces show no sign of the rust, like is visible in earlier die states.
Regular die wear was common throughout the years at the mint. But sometimes it became much more severe. The pressure exerted on the dies was so great, that it would literally shatter the dies. Over time, die cracks would form, where the die would literally be falling apart. Die cracks are usually located around the periphery and are precursors to partial and full cuds. Die cracks appear as raised lines on the coin and are usually ragged and of varying heights. Sometimes a die crack would run from one point on the rim to another point on the rim, and gradually becomes deeper, until a piece of the die literally fell off; this is called a cud. If the piece remains attached, but has a full crevice around it, this is called a partial cud. If the piece fell away from the die, this would then cause a blank, raised plateau like area to form on the coin where that piece fell away. This is called a full cud.
Die chips, or filled letters, were also a common form of die wear. This occurs when a piece of the die is chipped away inside a letter. This is common with the letters S, N, M, E, and F as well as the numerals 3 and 8. On the coin these areas appear filled in. These die chips often help determine the die state of a coin and are not connected with die cracks and cuds.
A hardened steel hub was used to transfer the main design of a coin onto a working die. The stars, letters, numbers, and other features were then manually punched into the die. Sometimes the engraver would make marks on the die to serve as a guide for where to make each punch. This process made each die a little bit different. These things allow us now to identify certain die marriages; that is the Obverse and Reverse die used together to make a coin. Some things to look for are repunches, which is when a design feature is punched a second time, and usually slightly off or rotated from the original punch. There are several examples of the numeral 3 being punched upside down, then repunched, making an 8 on the coin instead of a 3. We also can look at the distance of the design features from each other and the central design, as well as their relationship to the denticles of the coin. This method made each die unique and different in it's own way, unlike our current coinage, which is almost always identical from die to die.
Another problem with the mint, was under and over-weight planchets. The gold, silver or copper was melted into bars, and then flattened with rollers. Horses were used to pull a horizontal gear, which turned the rollers and flattened out the metal. The metal had to be sent through the rollers at least 10 times to reach the required thickness. A worker then took the piece of metal, and with a screw press, punched out proper sized pieces of metal, called planchets. The planchets were then weighed. Planchets that were too heavy were filed down until they were of the correct weight. This is a very common sight on silver Bust coins, and is usually seen as parallel scratch like marks. Sometimes it is very heavy and noticeable even after striking. Adjustment marks do not effect the grade of a coin, but often are not very appealing to the eye. If the planchet was underweight, it then went back to the beginning, and was melted down again and made into a new bar with more metal and taken through the process all over again.
I have come to the conclusion through my research, that the Mint was plagued with problems in its early years. The Mint had a lot to learn, and while they got help from knowledgeable people from outside the country, they still had a large learning curve to step up to, and in many cases had to learn the hard way. The mint has come a long way from its early years. Now, instead of only being able to make a few thousand coins in a year, the mint can make billions of coins, and are not as desperate for time and money as the fledgling first US Mint was.
One of the biggest problems the Mint had, was finding quality Tool Steel for dies. While we consider steel to be a very common material now, even as late as 1900, only a small percentage of iron mined was turned into steel, and even that was usually low quality and expensive. Phosphorus and sulfur were often a big problem in this steel. It would make the steel too brittle, and thus it would break very quickly, either during the process of making it into dies, or it would have terminal problems after striking only a few coins. Benjamin and William Huntsman of England, a father and son firm, created a process for making higher quality steel. They refined blister steel to make a more uniform and homogeneous steel. They also used Swedish iron, which was low in phosphorus and sulfur. This new steel was much more effective, but could still be prone to problems if the die was prepared wrong.
The making and preparation of a die was time consuming and expensive. So, the Mint did everything they could to salvage worn out dies. Old dies would be brought back up to the engravers. They would then lap it on a surface plate with a fine pumice or rottenstone with some cutting fluid. This was a very effective technique for removing clash marks and orange peel effect from the fields. Sometimes lapping made the first few coins struck with the die again appear proof-like. Sometimes, an engraver would get to aggressive with the lapping, and there would be loss of shallow details. This has been known to cause floating berries, shafts of arrowheads to disappear or appear thinner and loss of curl detail. Stars also appear to become smaller and farther apart from each other after lapping. If necessary, an engraver would also rework portions of the die to add lost details.
Rusting was also a problem when storing dies. Wax was commonly used as a rust preventative, but some dies still became rusted while in storage. This caused the dies to become severely pitted. Sometimes, a lapping would remove the pits and would make the last few pieces show no sign of the rust, like is visible in earlier die states.
Regular die wear was common throughout the years at the mint. But sometimes it became much more severe. The pressure exerted on the dies was so great, that it would literally shatter the dies. Over time, die cracks would form, where the die would literally be falling apart. Die cracks are usually located around the periphery and are precursors to partial and full cuds. Die cracks appear as raised lines on the coin and are usually ragged and of varying heights. Sometimes a die crack would run from one point on the rim to another point on the rim, and gradually becomes deeper, until a piece of the die literally fell off; this is called a cud. If the piece remains attached, but has a full crevice around it, this is called a partial cud. If the piece fell away from the die, this would then cause a blank, raised plateau like area to form on the coin where that piece fell away. This is called a full cud.
Die chips, or filled letters, were also a common form of die wear. This occurs when a piece of the die is chipped away inside a letter. This is common with the letters S, N, M, E, and F as well as the numerals 3 and 8. On the coin these areas appear filled in. These die chips often help determine the die state of a coin and are not connected with die cracks and cuds.
A hardened steel hub was used to transfer the main design of a coin onto a working die. The stars, letters, numbers, and other features were then manually punched into the die. Sometimes the engraver would make marks on the die to serve as a guide for where to make each punch. This process made each die a little bit different. These things allow us now to identify certain die marriages; that is the Obverse and Reverse die used together to make a coin. Some things to look for are repunches, which is when a design feature is punched a second time, and usually slightly off or rotated from the original punch. There are several examples of the numeral 3 being punched upside down, then repunched, making an 8 on the coin instead of a 3. We also can look at the distance of the design features from each other and the central design, as well as their relationship to the denticles of the coin. This method made each die unique and different in it's own way, unlike our current coinage, which is almost always identical from die to die.
Another problem with the mint, was under and over-weight planchets. The gold, silver or copper was melted into bars, and then flattened with rollers. Horses were used to pull a horizontal gear, which turned the rollers and flattened out the metal. The metal had to be sent through the rollers at least 10 times to reach the required thickness. A worker then took the piece of metal, and with a screw press, punched out proper sized pieces of metal, called planchets. The planchets were then weighed. Planchets that were too heavy were filed down until they were of the correct weight. This is a very common sight on silver Bust coins, and is usually seen as parallel scratch like marks. Sometimes it is very heavy and noticeable even after striking. Adjustment marks do not effect the grade of a coin, but often are not very appealing to the eye. If the planchet was underweight, it then went back to the beginning, and was melted down again and made into a new bar with more metal and taken through the process all over again.
I have come to the conclusion through my research, that the Mint was plagued with problems in its early years. The Mint had a lot to learn, and while they got help from knowledgeable people from outside the country, they still had a large learning curve to step up to, and in many cases had to learn the hard way. The mint has come a long way from its early years. Now, instead of only being able to make a few thousand coins in a year, the mint can make billions of coins, and are not as desperate for time and money as the fledgling first US Mint was.
-George
42/92
42/92
0
Comments
Liberty: Parent of Science & Industry
A DAMMIT BOY from Jonesy 1/25/05
Lieutenant, Covert Operations
Subcommittee
my first POTD award 7/16/05
the cat ate my blue fish.
Didn't wanna get me no trade
Never want to be like papa
Working for the boss every night and day
--"Happy", by the Rolling Stones (1972)
<< <i>George, great stuff. You are on fire! I cannot wait until tomorrow's installment.
I think I'm out of material now...
42/92
<< <i> There are several examples of the numeral 3 being punched upside down, then repunched, making an 8 on the coin instead of a 3. >>
Can you name one? I am not aware of any variety like that. The 1808 C-3 half cent has the final 8 made by using the 0 punch from the fraction on the reverse and overlapping the two punches. That is the only case I can think of where one digit punch was used to simulate another.
You also might want to make it clear on the weight adjustment of the planchets, that the adjustments were only made on the silver and gold planchets. Copper planchets were not individually weighed to check their weight.
Thanks for clearing that up about planchet adjustment
42/92
You are probably referring to an 1834 LM-1. Cool variety!
Also, thanks for the great article. That is some good work!! Our HR department (that's me) is still waiting to hear from you regarding the job offer. Hey.....it's your choice: clean toilets or clean coins while going through college.
Here's the next assignment: Nova Constellatio coppers.
Our eBay auctions - TRUE auctions: start at $0.01, no reserve, 30 day unconditional return privilege & free shipping!
42/92